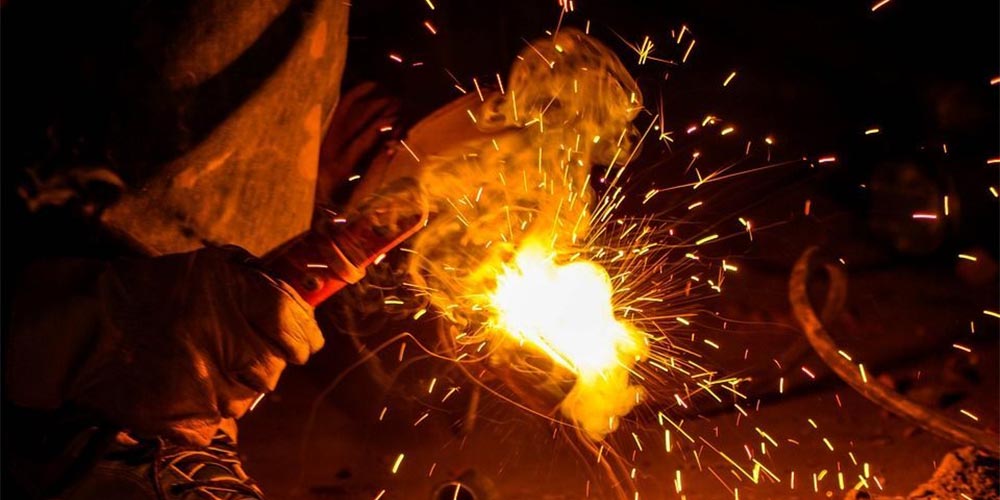
For those of you who have never seen or heard of a blast furnace, it is one of the most versatile and powerful welding processes around. In this process, the operator begins by igniting a magnetron by using alternating current and a spark plug which will create a flame. The arc causes the liquid to flow through the flame, which is actually what the operator desires to happen. The liquid flows from the flame in the manner of a stream, which in turn produces metal welds and other workable items. There are two main methods for welding, tube forming, and barrel forming. The particular type of these two welding processes is based on the kind of metal that is going to be melted.
Tube forming is often used for low melting welding because the metal that can be welded is smaller than the weld material itself. It is best to use two holes in the base of the tube with a steel sleeve in between. The base and the sleeve are welded together using a tube form. The first stage of the procedure will involve the operator creating a ring around the base, around the middle, and the top. Once this is done, the outer end of the tube will be welded to the base to form a tube. As it is completed, the operator will disconnect the tube from the area and seal the remaining edges with the solder. This will ensure that the tube can’t be broken while being welded.
After the inner and outer portions of the tube have been welded together, the operator will then weld the bottom portion. The flow of the liquid metal will continue until the workpiece is complete. If there are various areas to weld, the operator can use the tubes that the workpiece is made to link these areas together. Using a stanchion or a tube guide will make this possible. Both of these devices are similar, and they also help to make the process more accurate. To make sure that you are getting the best results from your tube forming or barrel forming endeavor, it is important to use a high-quality torch. Using the wrong torch can ruin your project by causing flare-ups, burns, and other accidents that can be avoided by using a torch that is designed specifically for tube forming and barrel forming.
Mig Welding On A Piece Of Brass Tubing
You may find it easier to do your MIG welding on a piece of copper or brass tubing. This is a popular choice among welders because the clearness of the glass is great and the weld bead is even. There are more tips and information at Weldingmachinereviews.com to check out. You can also use a larger section of tubing for your MIG welding project than you would for many other welding types. If you use thick tubing you will be able to get bigger welds so it is easier to get the job done. You may also be able to use a larger weld bead and make a more even joint.
The only problem with using tubing is that the parts may crack in some areas so you may need to lay the pieces down first before you install them together. You should use the same type of pipe as the connections are made to the parts. If the pipes are different then there is a good chance that you will not get an even weld. Keep in mind that you can make these connections on the work table and then when you finish the joint put the pieces back together. You can also make these joints on the welding bench. If you weld your parts on the bench then you can set them up and weld them on your work table.
The great thing about doing your MIG welding on a piece of brass tubing is that you will not have to worry about a seam rubbing against the other pieces. A bit of care and preparation will go a long way in making sure you get the welds properly joined together. You will want to heat the pieces so that the glass gets very hot before you join them together. The glass may still become cool so if you wait too long the weld may not be even.
Understanding the Different Types of TIG Welding
If you are just starting to investigate the options of becoming an apprentice or looking to take up this career path, there are many different types of tig welding that you can start with. You may be a novice in the welding field, or perhaps you have had training in the skill and would like to progress to the next level. There are different levels in this career where the skill set will vary according to the experience and education level that the person has. There are many different welders available with each branch or specialty, so there is sure to be one for your learning and skill level. To get the job done in the best possible way, you must learn all the parts of the welding process so that you can master it.
It is very important to familiarize yourself with the various types of welding and how they operate. Understanding the equipment used and how to operate it will save you money and time when you do have an important job to finish. One of the main things that you need to understand about the tig welding process is the heat transfer. The way heat is transferred into the metal piece you are about to weld will determine the quality of the end product that you create. The quality of the end product will depend on the quality of the process, as well as the tools used, and the knowledge of the person performing the welding. To be a good tig welder, you will need to understand the equipment and what to look for before you buy it.
When you are an apprentice or first-time welder, you are required to have certain courses, especially in the areas of flux capacitors and arc welding, and safety. This type of training will give you a better understanding of the different types of welds that you are likely to be required to do and which ones you should be able to do and which ones you need to ask someone else to do. The welding industry is very high-tech and requires skills to make welds that are long-lasting and stable. The final products can last many years and can even be passed down to future generations. You will need to know what type of equipment you will be using and what types of tools and supplies you will need for the job. The knowledge of the skill to be proficient in this type of welding can only come from years of experience and education.
Stick Welding – Understanding the Process
Stick welding was originally developed in the mid-1800s as a method of taking the lead and placing it inside a tube. Since there is no air or oxygen present, the lead solidifies into a metal. Once hardened, the metal can flow or curl which makes the metal extremely strong. It is also known as blow-molding and it is a very popular form of welding.
The other benefit of stick welding is that it has a unique and continuous flow system that allows for the use of several rolls of material with a single weld. This reduces the cost of the item that needs to be welded and gives the operator the ability to produce more jobs at one time. Many operators are amazed when they see the job that can be accomplished by a single roll of stick wiring alone. Because of the unique continuous flow system, stick welding can be combined with high voltage equipment. This equipment uses plasma sparks which are powered by high voltage electrical currents and allow for greater accuracy in the process of cutting, shaping, and finishing the pieces that need to be completed.
If you decide that stick welding is right for you and your needs, your work will consist of using the thin wires to reach welds. The process consists of applying a moderate amount of heat and to soften the material so that it will easily flow through the holes. A tool called a stick gun comes in handy and will work on both metals and non-metals. These tools are quite small and can be carried anywhere in the workplace. They can also be used as an improvised tool to complete multiple tasks that would otherwise be impossible to do. Stick welding is commonly used in the automotive industry as well as in the construction field. With the increased popularity of welding equipment, stick welding is quickly becoming a key item in the industry.